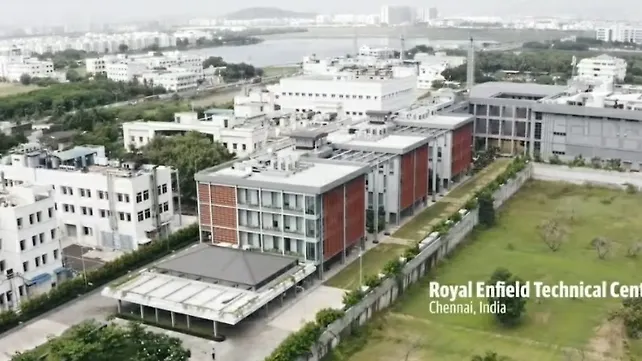
Royal Enfield has been in the news for pretty much everything, be it for their motorcycles, EVs, new riding gear, or the Himalayan Odysseys. It was recently in the news for their new Bullet 350, and it will continue to be so for a few more months, thanks to the upcoming Himalayan 450. But in this story, we will share some insights from our recent visit to Royal Enfield’s India Technical Centre. Some of these insights blew our minds and could blow yours, too.
This facility is somewhat new and houses the brand’s headquarters. It is situated in the hustle and bustle of Chennai and has attracted talent from all over India. As a part of the new Bullet 350 launch, BikeWale was invited to visit their India Technical Centre and J series factory. While this centre was quite big and had too many things to cover, we managed to get an idea of how Royal Enfield works behind the scenes and all that their bikes must undergo before hitting the roads. Even though we were not allowed to take our phones inside to take pictures, we managed to gather a great deal of information. Here are five things that amazed us at their new technical centre.
1: Design Studio
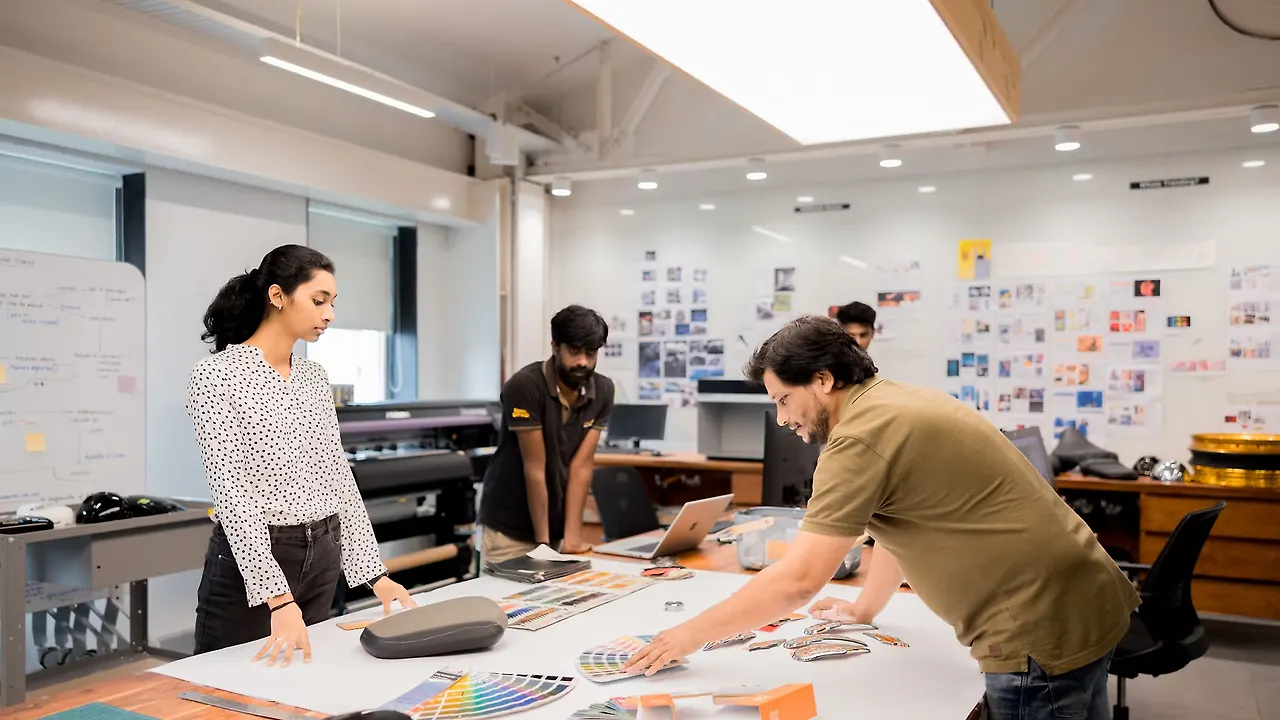
The industrial design studio is where the actual development of the motorcycle begins. Once this team gets data from the product planning team, Siva, the head of the studio, and his team work on creating the new bike. The studio was filled with bright lights, massive clay modelling equipment, lots of whiteboards, and some prototypes that were covered, sadly.
This is where we were also told about the journey of prototyping. Once the clay model is ready, the next step is to build a prototype with some of the cycle parts of the bike. The components used on this bike are mostly made using 3D printers. This prototype allows for a close representation of the final model. Once the data points are recorded and analysed, this model is then forwarded to the engineering team responsible for creating the actual motorcycle. This team’s goal is to build a bike that closely resembles the final production model. Some parts of the motorcycle are made by RE, and some come from their supply chain.
2: Testing
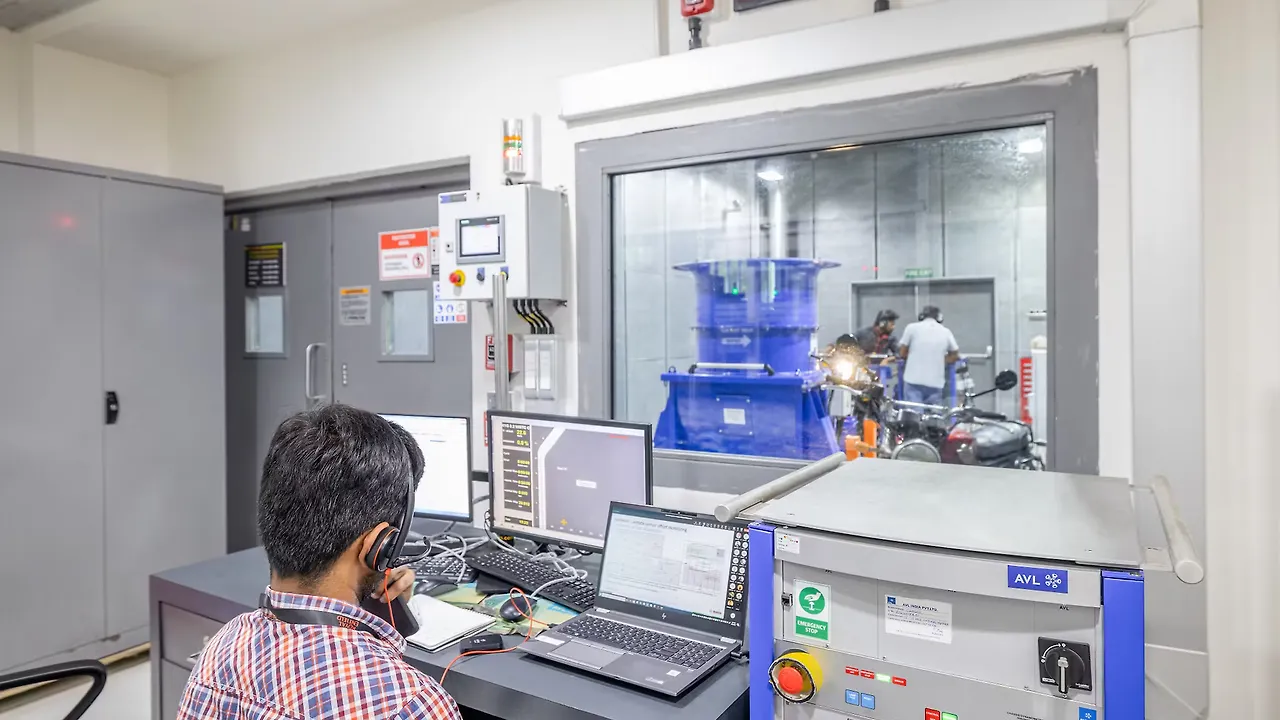
Just before the company decides to go into production, every single part that goes into making a motorcycle is tested thoroughly. Now for obvious reasons, Royal Enfield can’t test a bike for years. Thus, they have a series of equipment that accelerates the entire testing process. For example, this facility can do ten years of riding usage in just two to three months. Additionally, every motorcycle component has to go through many cycles of tests. Some cycles last for as long as 10,000 times. We saw testing rigs to test the durability of the side and main stands, along with the ignition key and grab-rails. Then, there were specific cold and hot boxes where instrument clusters and turn indicators were kept in extreme conditions. Every single brake and clutch lever had to go through weeks of testing.
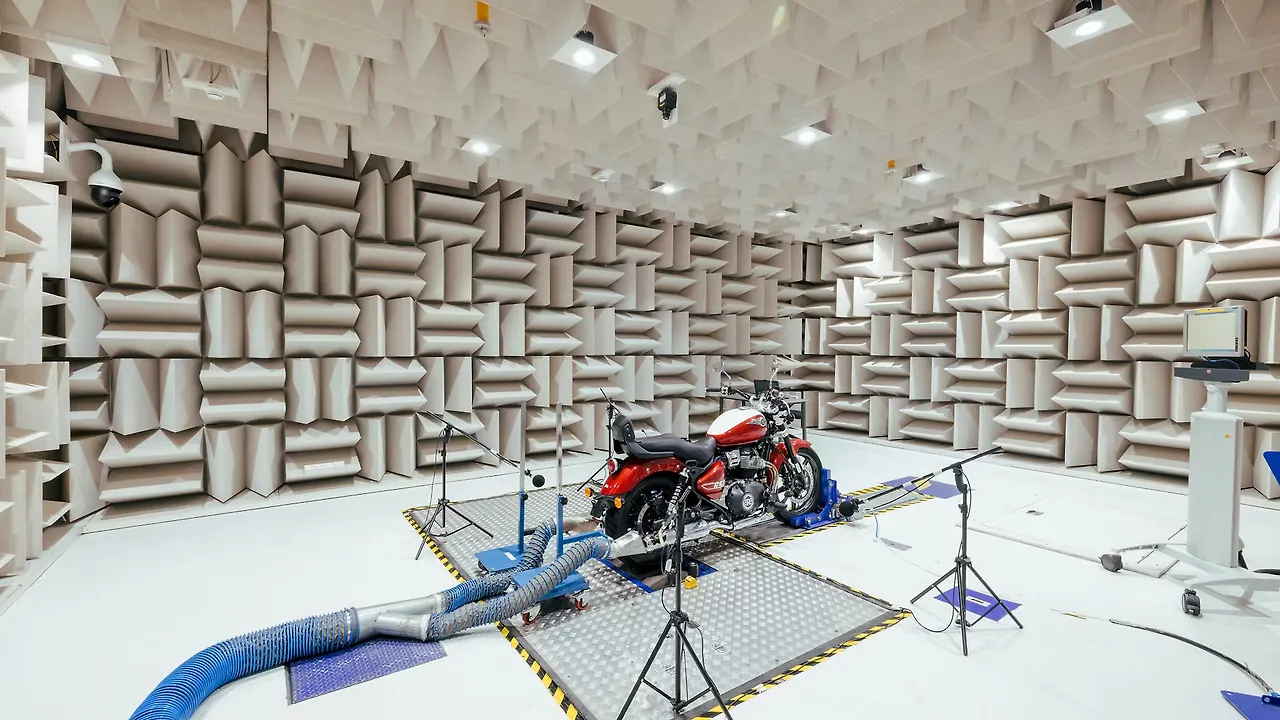
The main highlight was RE’s road testing rig, which occupies an entire room. Here, every motorcycle has to go through rigorous and continuous abuse. To give you a better perspective, a Super Meteor 650 was tested, and its front fork tubes were being compressed more than that of a Himalayan 411 during a massive jump. Imagine conducting this test 10,000 times.
3: Prototyping
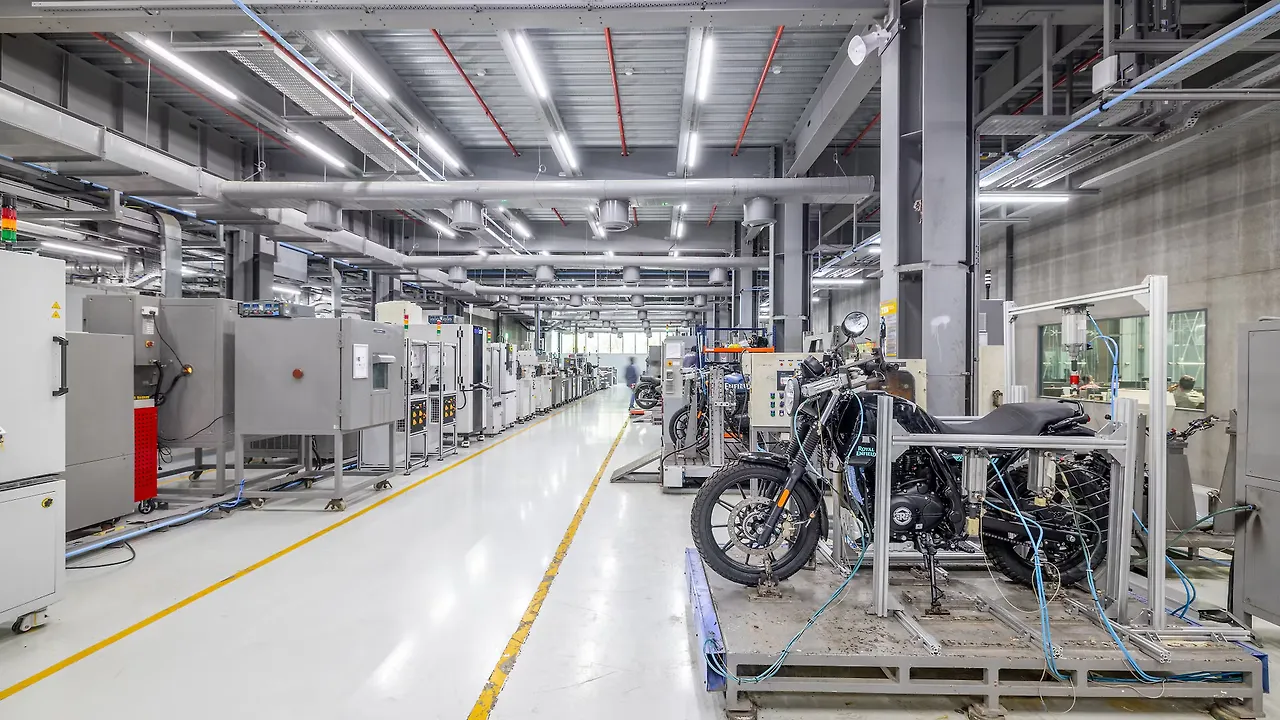
The prototyping at Royal Enfield happens behind closed as well as open doors. Once the design and engineering team have most things ready, the prototypes are built in various stages. The first two prototypes usually have a chassis, engine, and some cycle parts and basic body panels. After conducting a few testing cycles, these prototypes then get the actual production-ready cycle parts. This process helps the brand get closer to the final model that will be sold to the customers. Once these test mules have gone through road and rig testing, they are taken to the prototyping area. There, the engineers check the data and make appropriate changes before taking the prototypes to the road again. This process is repeated many times until the team is satisfied with the results.
4: Building
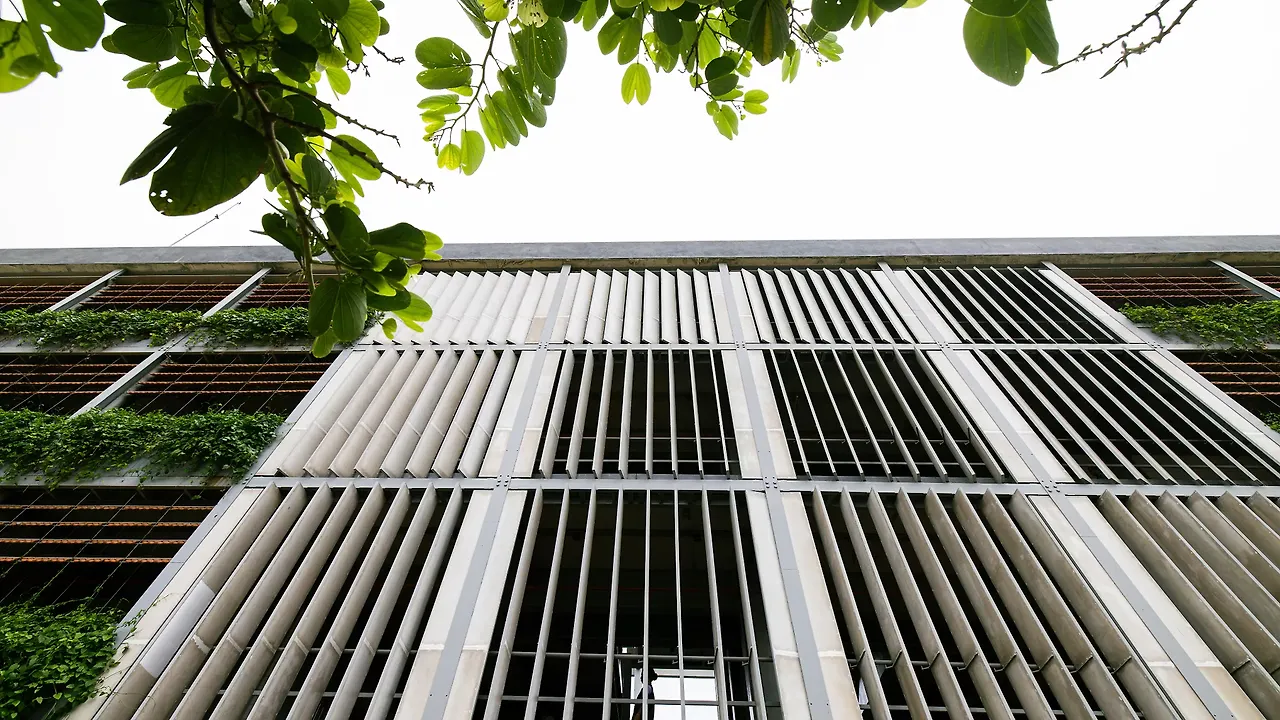
The RE HQ has divisions, and the main building is where most of the magic happens. The technical centre is unique and has a very open architecture. While certain sections of the facility are restricted to certain people, like the design studio, there are many places where people can sit and work openly. The centre of the building is open and doesn’t have any floors. The bottom of this floor is where the prototype motorcycles are made ready. The tooling and the preparations are also done here. Every single employee of the building can easily spot the happenings of this place. Then, the ground floor of this building houses the testing department due to the weight of the equipment. We were told that the majority of this equipment is not bolted to the ground, as it could send vibrations to the top floor.
5: Mindset
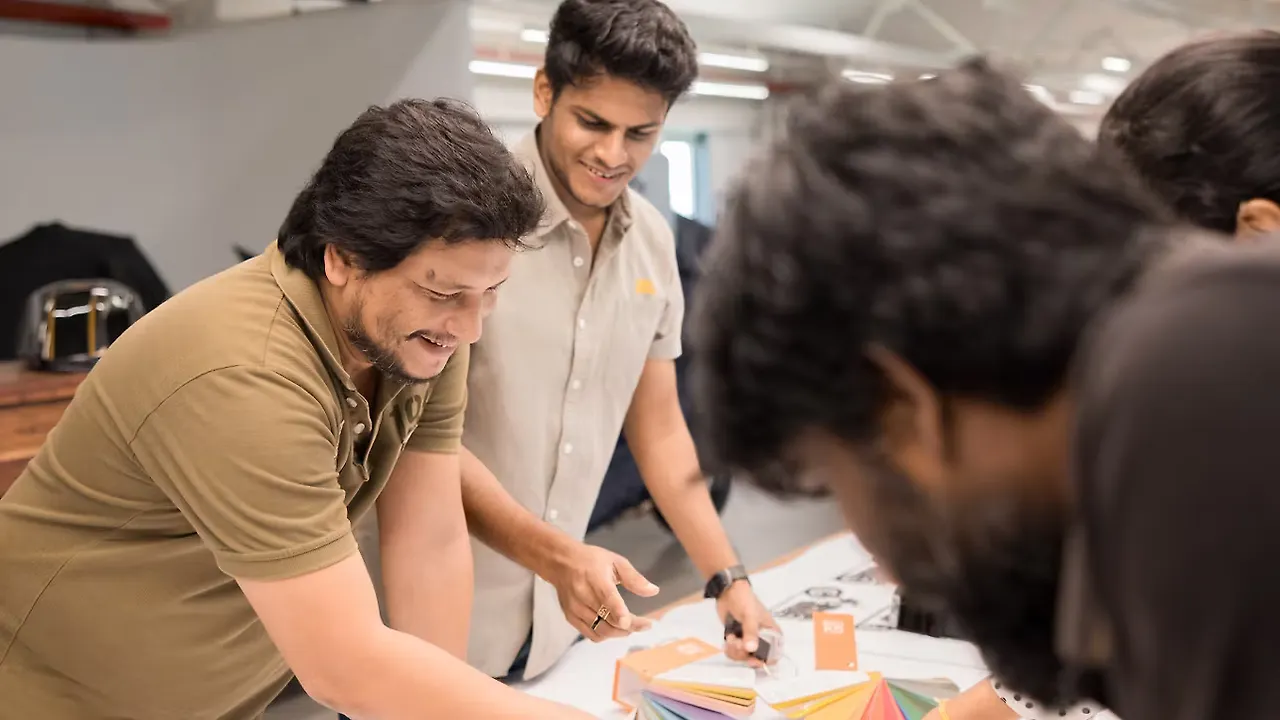
We spoke with multiple people from this facility and they all are passionate about motorcycles and the brand. Many of them go riding, which is an essential aspect of the motorcycle culture. In fact, we saw plenty of chairs and desks with jackets and helmets on them, which clearly showed a lot of passion. While most were a little apprehensive about talking to the journalists, a few were extremely happy to share their work experiences.